Warning this is NSFW (Not Safe For Wallet)! Your warranty and/or return options will be gone.
I'd buy a big hole saw and use the drill press for the fan hole (...or if you have a sexy mill, use that) - (... or 3d print). I did a much uglier jigsaw and vice method. The flow was;
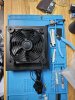
Remove these 8 screws to get to the top of case - from the inside.
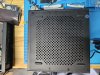
Mounting the fan from the inside once you're done making the hole (don't forget to paint any exposed metal).
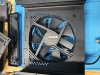
This is the hole to enlarge for your first mount.
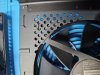
Hole size I ended up with after cut-out.
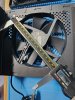
Here is a 3-way of MS-01, all up in each others business. So hawt!
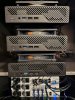
How loud is it with several switches and three MS-01 with 140mm fans? See below. This is 6" above the MS-01 (and mostly the switches).
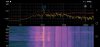
That is all I've got - enjoy your 140mm blow job! ;-p
- Remove the bottom case (8 screws) and drill two specific (noted below) top existing holes, slightly bigger for the fan's mounting screws.
- Use protection. Metal will be flying around now. The Jig Saw will be loud. E&E folks. (eyes & ears)
- Mount the fan using the two slightly bigger holes and use a Markal Silver-Streak Holder with Reflective Lead (the lead insert is skinny enough to mark the holes through the fan holes), to mark the holes for rear and trace the fan opening. Don't pick your nose or rub yours eyes now.. it is a lead insert. Wash you hands, swap your gloves, whatever you need to do.
- Drill the 2 rear holes and a bigger hole, near the edge of the fan opening trace line (for the jigsaw blade).
- Mount the case top in a vice and use the jigsaw with a bi-metal cutting blade, to cut out the fan opening. Pro-tip attach a bit of wood (using the screw holes) that sticks out further than the case. Use the wood to grip with the vise - to not mar the paint of the case. At the very least, use something (cardboard/rubber/etc.) to keep the vise's jaws soft.
- Paint the exposed steel (I used matte black Krylon Fusion) to prevent rust.
- Attach the fan mount screws from the inside, to the fan mounted on the outside of the case.
- Put the face-plate (falls off when you remove the bottom) and bottom, back on the case.
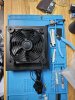
Remove these 8 screws to get to the top of case - from the inside.
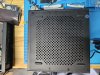
Mounting the fan from the inside once you're done making the hole (don't forget to paint any exposed metal).
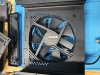
This is the hole to enlarge for your first mount.
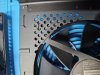
Hole size I ended up with after cut-out.
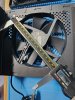
Here is a 3-way of MS-01, all up in each others business. So hawt!
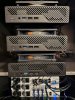
How loud is it with several switches and three MS-01 with 140mm fans? See below. This is 6" above the MS-01 (and mostly the switches).
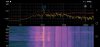
That is all I've got - enjoy your 140mm blow job! ;-p
Last edited: