A little overview, I have a large fileserver (17 drives but needing more) and most NAS cases are expensive or do not hold many drives, I currently have two fractal design XL R2's one with motherboard and some drives in it, the other with additional drives and a HP SAS expander so it functions as a JBOD.
I have been musing 3d printing some kind of case just to hold more drives of which this is now starting to come true!.
Build bullet points
2020 Aluminium profile for framework
3d printed drive cages
3d printed drive caddies
3d printed side panels/front and rear
3d printed brackets for holding PSU and other small parts.
Spec of each unit before my hardware is installed which is currently 11 8TB drives, 6 4TB and 2 400GB SSD
JBOD
24 3.5" drives spread across 6 drive cages
HP SAS Expander (I have them already)
Drive cage will be using a HP 466509 4 drive SAS backplane as it is molex so no wiring faff.
Front to back airflow with 140mm fans in the front panel aligned with where the drive cages are
PSU ATX format (I have corsair HX850 and 1050 available, stupidly overkill for these but its what I have available as already own them)
Server
8 3.5" drives spread across 2 drive cages
?? 2.5" drives (these will be for cache and also due to size constraints)
ATX or smaller motherboard (I have a supermicro X9SRL-F)
Front to back airflow
3D Printing
A majority of this other than the frame will be 3d printed, small brackets and such for securing parts will also be printed, due to the company in the UK 3DQF I can get end of colour run PLA for £12 per 1KG spool but its random colour choice which is not a big deal for this as it will end up being painted anyway.
Approx print times are below
Drive cage for 3.5" drives 20 hours, 240g filament
Drive Caddy for 3.5" drives 2hr 20, 27g filament
Frame is 450mm deep, 380mm high and 315mm wide, with the 3d printed side panels it will end up around 460mm deep, 400 high and 325 wide, it is just a coincidence this is themed off a Sun E450 and happens to be that the frame is 450mm deep, I do not think I will be able to make ensure case with panels be 450 deep without restricting cable access between the drive cages but i will be trying as it is a happy coincidence and adds extra nerdery
Colour codes RAL 4005, RAL 7040 and RAL 7015 for the purple/lilac, dark grey and light grey (light grey interior) so will approx match the genuine E450
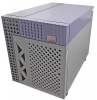
Ignore the holes in some of the cross members thats just a remnant of my Fusion 360 work, top of case has the 2040 profile as I intend to stack the server version ontop of the JBOD version so wanted some extra strength just incase
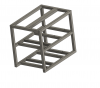
JBOD version will look roughly like this though exact placement of the drive cages is to be determined, I am intentionally having space inbetween them to allow for access to the cabling, PSU could be mounted flat too but in this orientation allows plenty of space for rear panel vents on the top section and PCI slots (SAS expander, fan controller etc)
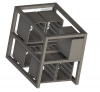
Server version, big box is ATX motherboard, drive cages are too deep to comfortably be next to the motherboard
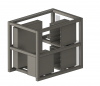
Case panel idea, due to limited print bed size doing it in small chunks like this will be best, also means i could make it so just the section in picture is removable for access to the backplane/cabling.
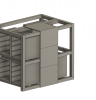
Drive cage mockup V0.05
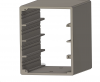
Drive Cage V0.07, Channels in the side slightly revised to have a chamfered edge, these channels will be used for holding the 3mm fibre optic light to transfer the backplanes LED to the front of the cage as they will not be in the drive caddy itself, also slight tweak to the bolt hole placement on the left side, holes are designed to take 6/32 UNC (Hard drive/case screw) for commonality and also the fact I have a shedload of them for this.
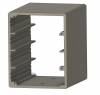
Drive caddy V0.08, probably way thicker material than needed but its not a lot of filament and fast to print
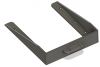
Currently as of er noon on the 6th November, the drive cage is printing but can show the below pics of things during testing phase.
Backplane on a cut down version of the drive cage to see how things fitted
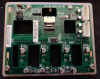
Design has been slightly tweaked since to move the channels to line up with the LED's, small brackets will be made to hold the end of the fibre optic
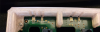
Fiber optic bracket in question, lil dab of hotglue to secure the fibre and allows for exact lining up as required.
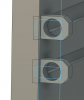
I have been musing 3d printing some kind of case just to hold more drives of which this is now starting to come true!.
Build bullet points
2020 Aluminium profile for framework
3d printed drive cages
3d printed drive caddies
3d printed side panels/front and rear
3d printed brackets for holding PSU and other small parts.
Spec of each unit before my hardware is installed which is currently 11 8TB drives, 6 4TB and 2 400GB SSD
JBOD
24 3.5" drives spread across 6 drive cages
HP SAS Expander (I have them already)
Drive cage will be using a HP 466509 4 drive SAS backplane as it is molex so no wiring faff.
Front to back airflow with 140mm fans in the front panel aligned with where the drive cages are
PSU ATX format (I have corsair HX850 and 1050 available, stupidly overkill for these but its what I have available as already own them)
Server
8 3.5" drives spread across 2 drive cages
?? 2.5" drives (these will be for cache and also due to size constraints)
ATX or smaller motherboard (I have a supermicro X9SRL-F)
Front to back airflow
3D Printing
A majority of this other than the frame will be 3d printed, small brackets and such for securing parts will also be printed, due to the company in the UK 3DQF I can get end of colour run PLA for £12 per 1KG spool but its random colour choice which is not a big deal for this as it will end up being painted anyway.
Approx print times are below
Drive cage for 3.5" drives 20 hours, 240g filament
Drive Caddy for 3.5" drives 2hr 20, 27g filament
Frame is 450mm deep, 380mm high and 315mm wide, with the 3d printed side panels it will end up around 460mm deep, 400 high and 325 wide, it is just a coincidence this is themed off a Sun E450 and happens to be that the frame is 450mm deep, I do not think I will be able to make ensure case with panels be 450 deep without restricting cable access between the drive cages but i will be trying as it is a happy coincidence and adds extra nerdery
Colour codes RAL 4005, RAL 7040 and RAL 7015 for the purple/lilac, dark grey and light grey (light grey interior) so will approx match the genuine E450
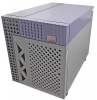
Ignore the holes in some of the cross members thats just a remnant of my Fusion 360 work, top of case has the 2040 profile as I intend to stack the server version ontop of the JBOD version so wanted some extra strength just incase
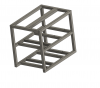
JBOD version will look roughly like this though exact placement of the drive cages is to be determined, I am intentionally having space inbetween them to allow for access to the cabling, PSU could be mounted flat too but in this orientation allows plenty of space for rear panel vents on the top section and PCI slots (SAS expander, fan controller etc)
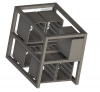
Server version, big box is ATX motherboard, drive cages are too deep to comfortably be next to the motherboard
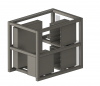
Case panel idea, due to limited print bed size doing it in small chunks like this will be best, also means i could make it so just the section in picture is removable for access to the backplane/cabling.
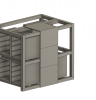
Drive cage mockup V0.05
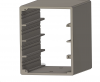
Drive Cage V0.07, Channels in the side slightly revised to have a chamfered edge, these channels will be used for holding the 3mm fibre optic light to transfer the backplanes LED to the front of the cage as they will not be in the drive caddy itself, also slight tweak to the bolt hole placement on the left side, holes are designed to take 6/32 UNC (Hard drive/case screw) for commonality and also the fact I have a shedload of them for this.
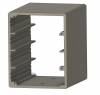
Drive caddy V0.08, probably way thicker material than needed but its not a lot of filament and fast to print
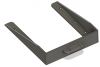
Currently as of er noon on the 6th November, the drive cage is printing but can show the below pics of things during testing phase.
Backplane on a cut down version of the drive cage to see how things fitted
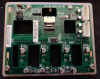
Design has been slightly tweaked since to move the channels to line up with the LED's, small brackets will be made to hold the end of the fibre optic
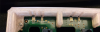
Fiber optic bracket in question, lil dab of hotglue to secure the fibre and allows for exact lining up as required.
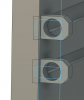
Last edited: